DOWNDRAFT TABLES
Built-In Fume Extraction for Manual Cutting and Grinding
Capture dust and particulate at the source with heavy-duty downdraft tables from VentBoss. Downdraft tables or benches are especially well-suited for capturing heavy particulate from manual cutting, grinding and metalworking. The right downdraft workstation can help you keep the work area clean, reduce worker exposure to harmful dust, and ensure regulatory compliance with worker safety regulations.
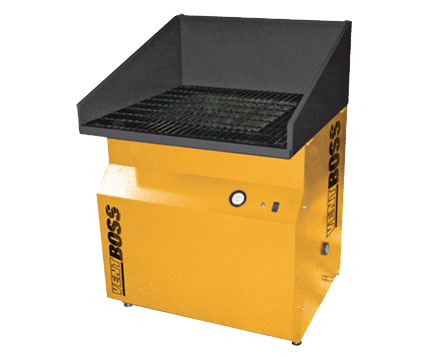
PLUG-AND-PLAY DOWNDRAFT TABLES FROM VENTBOSS
Downdraft tables from VentBoss are designed to meet the needs of fabrication shops, technical schools, and anyone needing dust and fume extraction for light- to medium-duty applications. These units combine exceptional durability with simplicity and ease of use, so you can just plug them in and get to work.
- Heavy-duty, all-steel construction with steel bar grate worksurface
- Simple setup and plug-and-play operation
- Nanofiber MERV 15 filtration
- Compressed air filter cleaning for maximum filter life
- Built-in spark arrestance to keep sparks out of the filter chamber
- Acoustic silencing to minimize noise and ensure operator comfort
- Drop-down side screens (S210 and S211)
FIND YOUR DOWNDRAFT APPLICATION
Fabrication shops working with metals would find a downdraft table beneficial. Grinding, metal cutting, polishing and other fabricating applications can produce dust and fine particulates. Downdraft tables draw these contaminants away from the worker and into a filtration system to protect workers and ensure a safe working environment. Downdraft tables are compact and versatile, so they are easy to fit into most fab shop environments.
Technical and vocational schools that teach skills in metalworking, and other hands-on trades and crafts can significantly benefit from downdraft tables. The tables can provide students with a safe learning environment by reducing airborne contaminants created during cutting, grinding, sanding, and finishing of small parts. Easy setup and plug-and-play operation are a plus in an educational environment.
Art studios, maker spaces and community workshops have become increasingly popular for hobbyists, designers, and entrepreneurs. These shared spaces for creators and hobbyists can have a variety of tools and equipment for building, designing and prototyping. Incorporating downdraft tables for activities such as cutting, grinding and polishing can ensure a safer environment for everyone.
FREQUENTLY ASKED QUESTIONS ABOUT DOWNDRAFT TABLES
Downdraft Tables
Downdraft tables are widely used in industries like metalworking and general fabrication to control dry dust and particulate created during cutting, grinding, sanding and finishing. Downdraft tables not only enhance workplace safety by reducing respiratory risks but also contribute to cleaner work areas, improved product quality, and regulatory compliance. They are an excellent general-purpose workstation and dust collection system for a variety of manual applications. Workers can simply place their pieces on the workbench, turn on the integrated downdraft filtration system, and get to work.
Downdraft tables are generally recommended for light- to moderate-duty manual applications producing larger, heavier particulate. While they are sometimes used for weld fume collection, other fume collection options may be better for welding or other applications producing rising thermal fumes. Downdraft tables are also not recommended for applications producing highly toxic fumes (like stainless steel metalworking) or utilizing metalworking fluids. NFPA 484 allows the use of downdraft benches for collection of potentially combustible metal dust as long as the total dust collected each day is less than 0.5 lbs.
Downdraft tables or benches are sometimes used for welding, but they are not always the best option. For welding and other thermal applications that produce submicron particulate, a backdraft table is usually preferred. That is because weld fumes rise as they are created. A downdraft table, which creates a downward airflow, may miss fumes that rise too quickly to be captured. These fugitive weld fumes end up in the welder’s breathing zone or escape into the wider facility. Downdraft tables may also present a fire risk when used for welding.
A downdraft table works by creating a flow of air that pulls particles, fumes, and other airborne contaminants downwards, directly away from the work area and the person using the table. Here’s a step-by-step breakdown of how it operates:
- Perforated Work Surface: The top of a downdraft table typically features a perforated or grated surface. This design allows for air to be uniformly pulled through the entire surface area of the table.
- Extraction System/Blower: Beneath the work surface, the table is equipped with a built-in extraction system, which creates a downward airflow.
- Capture of Contaminants: As the worker performs tasks like sanding, grinding, cutting, or welding on the table’s surface, the airborne contaminants produced are immediately drawn downwards by the airflow.
- Filtration System: Below the work surface and integrated into the downdraft table is a filter or series of filters. As the air carrying the contaminants is drawn down, these filters trap and capture the contaminants, preventing them from reentering the workspace or being released outside.
- Collection or Disposal: Some downdraft tables may have collection trays or bins to gather heavier particles, such as sawdust or metal shavings. Periodic emptying and cleaning of these trays or bins are necessary.
- Recirculation or Exhaust: After filtration, the cleaned air can either be recirculated back into the room or, in cases where there are harmful fumes, vented outside.
- Maintenance: For the table to remain effective, regular maintenance is essential. This includes cleaning or replacing filters, emptying collection bins, cleaning the grates on the work surface, and checking the motor/blower for proper functioning.
Downdraft tables and backdraft tables are both designed to capture and extract airborne contaminants during various tasks. The key difference lies in the airflow direction. In a downdraft table, air is pulled downwards through a perforated or grated surface, making it ideal for operations producing heavy particulates like sanding or grinding. On the other hand, a backdraft table directs air horizontally from the front to the back, capturing rising fumes, which makes it suitable for tasks like welding where fumes ascend. The choice between them depends on the specific nature of the work and the contaminants produced.
Downdraft tables are a simple, versatile and effective solution for control of dust and particulate created by manual metalworking and fabrication. They provide an all-in-one option for dust control, integrating a work surface with filtration and eliminating the need for a separate dust collector and ductwork. They also help keep the work environment safe and clean by collecting particulate at the source. Benefits include:
- Easy installation, with no ductwork required
- Compact, space-saving design that fits easily into the work environment
- Cleaner work environment and reduced time spent on housekeeping
- Improved air quality and enhanced worker health and safety
- Regulatory compliance
Downdraft tables require regular maintenance to ensure that they function optimally and provide a safe working environment. A poorly maintained downdraft table will not provide effective air filtration and can become a fire risk as particulate builds up on the grate and in the filters. Always refer to the manufacturer’s maintenance guidelines for specific recommendations and intervals. They will provide detailed instructions tailored to the particular model of the downdraft table. Typical maintenance tasks may include:
- Change filters: Check the filters regularly for loading, wear, or damage. Over time, filters will become saturated with captured contaminants. A compressed air filter pulsing mechanism can extend the life of downdraft table air filters.
- Surface cleaning: The grated surface of the table should be cleaned regularly to ensure consistent airflow and prevent the buildup of potentially flammable debris. Remove any debris or buildup that might block the perforations.
- Clean spark traps: If the system comes with built-in spark arrestance, the spark control system must be cleaned regularly to prevent the buildup of grime.
- Empty dust tray/containment: The downdraft table may come with a dust tray that needs to be emptied regularly or a particulate clean-out area that must be swept or vacuumed out.
- Motor/blower maintenance: Fans or blowers might require cleaning, lubrication, or, in some cases, replacement parts.