THE COMPLETE GUIDE TO WELDING
FUME EXTRACTION SYSTEMS:
HOW (AND WHY) TO KEEP YOUR FACILITY AIR CLEAN AND SAFE
CHAPTER FOUR: SOURCE CAPTURE SYSTEMS FOR WELD FUMES
Source capture is considered to be a best practice for weld fume collection and is preferred wherever possible. Source capture systems collect contaminants close to the source where they are produced, keeping them out of the breathing zone for manual welders and preventing the propagation of weld fumes throughout the facility. Source capture fume collection systems may be contrasted with ambient capture systems, which clean air for the whole facility. Most source capture systems use air filtration to filter fume and particulate out of the air. Cleaned air may be exhausted outside or returned to the facility (if certain criteria are met).
What is a source capture system for fume collection?
A source capture system collects contaminants from close to the source where they are produced. This may be accomplished via the use of hoods or enclosures that contain fume-producing processes or localized capture methods (such as fume arms) that pull weld fumes in as they are produced to prevent propagation through the facility.
A source capture system consists of the following basic elements: a capture hood, duct system, fan (blower) and exhaust ductwork. In a filtration source capture system, the hood is ducted to a dust collector that captures and filters the air to remove contaminants.
Is source capture required for weld fume extraction?
Source capture is not mandated for weld fume control, but it is recommended in most circumstances, especially for high-production welding environments and manual welding. Source capture prevents weld fumes from entering the breathing zone or moving throughout the facility, resulting in safer, healthier air.
What source capture methods are used for robotic welding?
For robotic welding, the entire process can be contained under a large hood or enclosure. Weld fumes are contained within the hood and exhausted or collected by a dust collector or wet filtration system. The hood should be designed to contain the particulate within the cell and not allow it to escape into the facility. No employees should be working inside the hood.
In some cases, the robotic welder may be equipped with a tip extraction hood that collects a majority of weld fume as it is created at the weld seam. This can be a useful alternative if the welder cannot be easily enclosed under a hood or if overhead cranes or other equipment are required. The amount of fume collected by this method may vary depending on the welding process and the way the robot moves. In some cases, it may be desirable to combine a tip extraction system with an ambient system to collect fugitive fume.
What source capture methods are used for manual welding?
Source capture for manual welding must pull weld fume away from the breathing zone of the welder. For this reason, the large hoods and enclosures used for robotic welders are not appropriate for manual welding. There are several source capture options for manual welding.
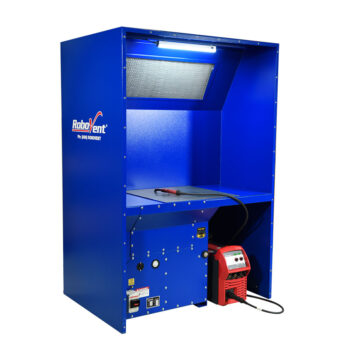
Backdraft Tables/Booths
A backdraft (or sidedraft) table or booth uses an intake plenum that is positioned to pull weld fume back and away from the welder’s face. The plenum may be combined with a work surface or booth for an all-in-one workstation and weld fume collection system. Backdraft tables are a good choice for smaller weldments that fit on the work surface. Unlike fume arms, they do not require any repositioning. Note: Downdraft tables, which pull air down rather than up, are not generally recommended for weld fume; because weld fume rises, downdraft tables may miss a portion of fume that rises beyond the reach of the extraction system before it can be collected. When using backdraft systems, make sure that the plenum is close enough to the weld fume source for efficient capture.
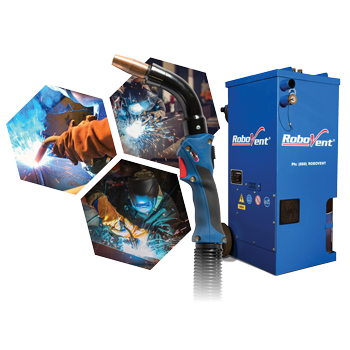
Fume Extraction Guns/Torches:
A fume gun (or extraction torch) combines fume collection with the welding torch itself. A fume gun has a small hood integrated into the tip of the weld torch, which is attached via a hose to a dust collection system. The best fume guns may capture between 90-95% of weld fume at the source; however, actual capture rates will depend in part on the technique used by the welder and the position of the torch. Hood position and airflow velocity for the capture system must be carefully calibrated to ensure efficient capture without disrupting the shielding gases. A fume gun can be a good option for large weldments or enclosed areas where other methods of source capture are impractical. Used correctly, it ensures efficient fume capture with little or no effort on the part of the welder and little or no impact on weld seam quality or welder comfort. Fume guns are only used with MIG welding.
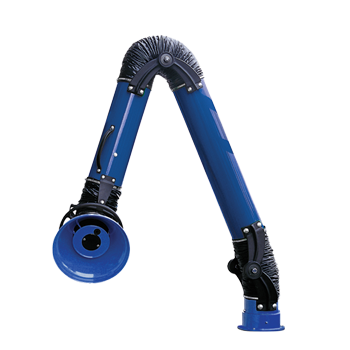
Fume Arms
Fume arms are mobile arms with a small hood on the end that is positioned over the weld seam. It is important to ensure that the fume arm is always correctly positioned to pull weld fume as it is created; this may require the welder to reposition the arm several times if working on a larger piece. Fume arms are a practical and flexible source capture option that can be used with either smaller tabletop pieces or larger weldments.
How can fugitive fume from welding be captured?
Even with an efficient source capture system, there may still be a problem with fugitive weld fume in the facility. Fugitive weld fume commonly results from improper positioning of a fume arm, the use of smoking/cooling bins for cooling parts, or fumes rising from hot weld seams after a fume arm or fume gun has been repositioned. Make sure fume arms are properly positioned over the weld seam for maximum fume capture. Overhead hoods can also be designed to better capture rising fume from smoking parts. If the hood or enclosure does not fully capture all weld fume, a secondary ambient air filtration or general ventilation system may be needed to remove the remaining fume. Not sure where to start? Learn More About RoboVent Facility Testing and Engineering Services.
TALK TO AN EXPERT
Want to learn more? Talk to a dust, mist and fume expert today by filling out the fields below.