The Heavy Equipment Market Is Heating Up. We’re Ready.
Heavy equipment manufacturing presents some of the toughest air quality challenges in the industrial world. To stay competitive and compliant, manufacturers must tackle these health, safety and environmental emissions issues head-on. As the industry evolves, RoboVent is helping manufacturers build a cleaner, safer future—one breath at a time.
The heavy equipment industry has been booming over the last several years. Driven by infrastructure projects, energy development and urban expansion, manufacturers of large construction, mining, transportation and agricultural equipment have been ramping up production at a rapid pace. From bulldozers to bucket trucks, the machines that shape the modern world are in high demand, and manufacturers are working hard to keep up.
Read Part 2 of this series: Solutions for Heavy Equipment Manufacturing.
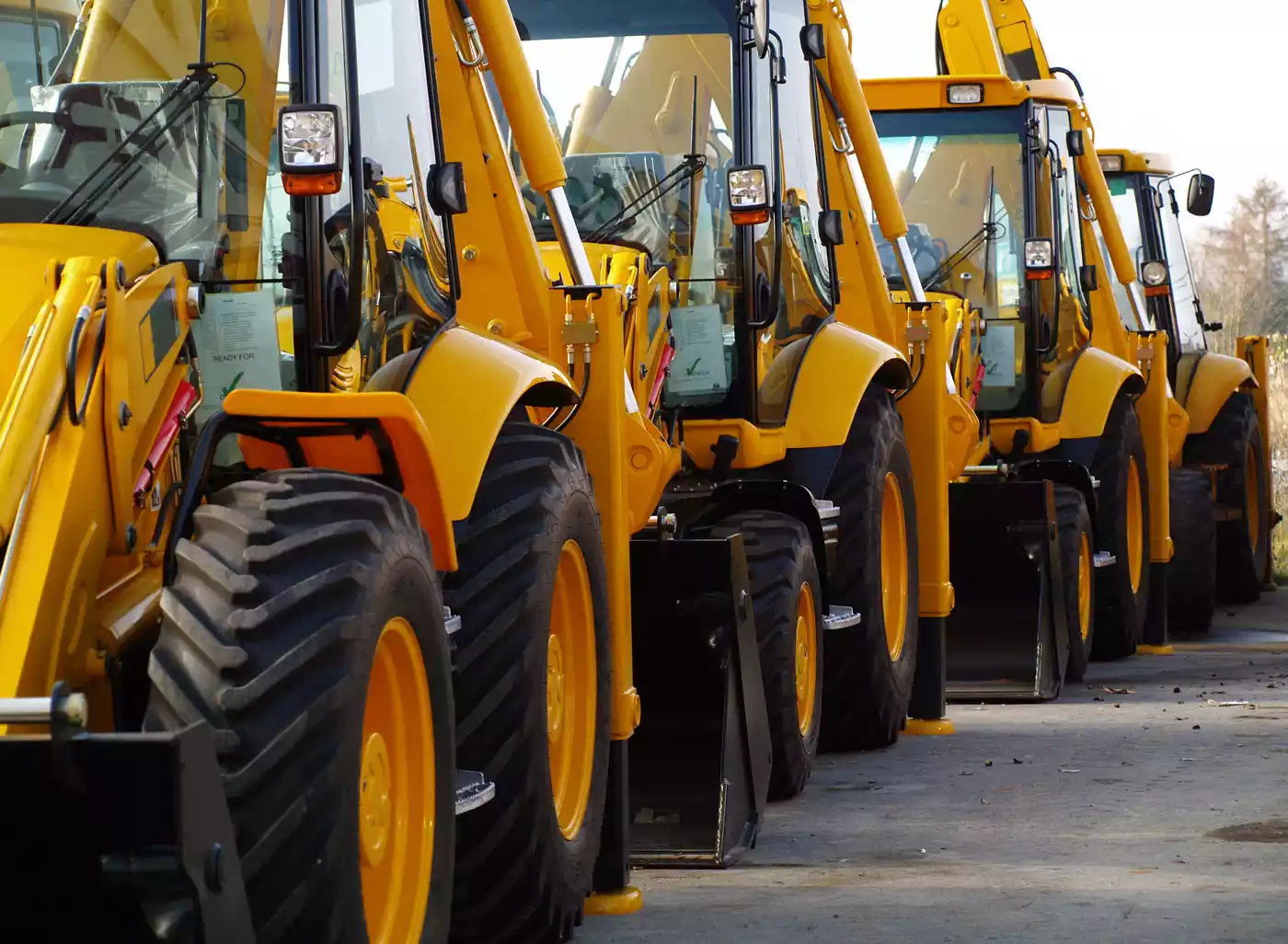
The heavy equipment market includes large machinery for construction, mining, transportation and agriculture.
Industry Trends in the Heavy Equipment Market
Heavy equipment manufacturers are navigating a period of rapid change and expansion. Market growth, electrification and reshoring are transforming the way equipment is designed, built and delivered. Here’s what we’re seeing.
- Market growth is strong. The U.S. heavy equipment market was valued at $44.7 billion in 2023 and is projected to grow to $57.1 billion by 2029, driven by infrastructure investment, mining, and energy development. Manufacturers are expanding capacity to meet rising demand across construction, agriculture and resource extraction sectors. New federal infrastructure spending, the transition to renewable energy and demand for new residential, commercial and industrial development are all fueling capital investment in equipment for earthmoving, material handling and land development. However, manufacturers face challenges such as rising costs for imported components due to tariffs, which may impact hiring plans and operational strategies. (Note: As of April 2025, it is unknown how more recent economic trends may shift growth trajectories for the industry.)
- Reshoring momentum continues. Supply chain disruptions, geopolitical instability and renewed focus on domestic industrial resilience has kept reshoring high on the agenda for many U.S. manufacturers. Some are considering investments in new or expanded production facilities in the U.S. to reduce dependence on overseas suppliers. Tariffs on imported parts and components may further accelerate reshoring, particularly among Tier I and Tier II suppliers. This shift is increasing demand for skilled labor and infrastructure improvements to support modern manufacturing.
- Electrification is transforming product lines. OEMs are rapidly developing electric and hybrid construction machinery to meet regulatory and sustainability targets. This shift not only changes the nature of the equipment itself, but also alters manufacturing requirements and production processes, from welding and assembly processes to facility layouts and worker training.
- Battery production is booming. The shift to electric heavy equipment is driving parallel growth in lithium-ion battery manufacturing for construction equipment. The North American market is expected to grow at a CAGR of over 17% through 2032, bringing increased demand for battery manufacturing facilities and materials handling infrastructure.
- Digital integration is transforming manufacturing. While technologies like robotic welding and CNC machining are well established, manufacturers are increasingly integrating them into fully connected, data-driven production environments. Smart sensors, real-time monitoring, predictive maintenance, and cloud-based analytics are helping plants boost efficiency, reduce downtime, and make more informed decisions across the production lifecycle.
- Environmental policy is in transition. Recent years saw a push toward stricter emissions regulations and sustainability goals, but the regulatory landscape is shifting under the new administration. While some federal standards may be revised or rolled back, many manufacturers are continuing to invest in cleaner technologies and processes, driven by state-level policies, international requirements and customer expectations around ESG performance.
Air Quality Challenges in Construction Equipment Manufacturing
As equipment manufacturers expand their domestic production capacity—whether building new facilities or upgrading aging ones—air quality and worker safety must be top of mind. The heavy equipment industry presents some of the most demanding environments in industrial manufacturing, with unique challenges compared to those found in high-volume, small-part production. These challenges are shaped by the size and nature of the workpieces, the materials being used and the specialized processes required to cut, weld and assemble massive steel structures.

Manual welding, grinding and cutting of large, heavy steel components produces dangerous dust and fumes.
- Working on large, heavy components poses unique airflow and capture challenges. From excavator booms to mining truck chassis, heavy equipment parts are often too large to be enclosed or worked on in fixed positions. Welders and fabricators must be mobile, moving around and under multi-ton assemblies. This makes source capture difficult, as fume arms and backdraft plenums can’t follow the work, and pieces may be too large for traditional hoods and enclosures. At the same time, the size and shape of the parts can interrupt airflow patterns, allowing dangerous fumes and particulates to linger.
- Material handling infrastructure limits system design. Overhead cranes are essential in these facilities, constantly moving large components across bays. That means ventilation systems must work around cranes, not obstruct them, ruling out certain duct layouts or hood designs. In facilities with high ceilings and open floorplans, this creates additional complexity for airflow control.
- Specialized cutting methods generate intense fume loads. Processes like hand-held plasma cutting, oxy-fuel torch cutting and thermal lancing are commonly used to shape or dismantle large pieces of steel. These methods generate dense metal fumes, fine particulates and hot slag, often in open environments with limited containment. Cutting operations performed on large structures—especially when workers are kneeling, crawling or cutting overhead—are difficult to ventilate effectively with localized capture.
- Materials create health risks. Stainless steel, chromium alloys and high-performance coatings introduce hazardous byproducts into the air. Welding on stainless steel, for example, creates hexavalent chromium, a known carcinogen subject to strict OSHA exposure limits. Coated or painted components may release volatile organic compounds (VOCs) or toxic fumes during welding, cutting or prep work. Heavy-gauge carbon steel, common in structural and load-bearing components, can also produce significant volumes of metal fumes during prolonged or high-amperage welding operations, increasing exposure risks for workers.
- High-throughput production increases exposure risks. As facilities move to more automation or multi-shift operations to meet market demand, workers may face prolonged or repeated exposure to airborne hazards. Even short-term operations like grinding or tack welding, when multiplied across dozens of stations and hundreds of parts, can create significant cumulative health risks if not properly controlled.
Legacy buildings weren’t designed for modern air quality standards. Many manufacturers are operating in facilities built decades ago, long before today’s standards for dust and fume control. Retrofitting dust collection and fume control for these plants to meet modern OSHA, EPA and NFPA guidelines is a complex but necessary task, especially when modernizing production lines or onboarding new materials and methods.
Addressing Air Quality Challenges in Heavy Equipment Manufacturing
Heavy equipment manufacturing presents unique air quality challenges that often require customized solutions. Large weldments, mobile work and overhead crane systems can make source capture difficult, calling for approaches like ambient air filtration or on-torch fume extraction. Facilities working with stainless steel and other hazardous materials may also need advanced filtration technologies to maintain compliance with OSHA and EPA standards.
Every facility is different, and effective dust and fume control starts with understanding the specific processes, materials and layout involved. A one-size-fits-all approach rarely works in environments as complex and variable as heavy equipment manufacturing.
Need help designing a clean air strategy for heavy equipment manufacturing? Contact the experts at RoboVent.
Contact Us With Your Questions!
SUBSCRIBE TO
BLOG UPDATES