Hand Plasma Cutting Dust and Fume Control
Supporting Clean Air Compliance in Heavy Equipment Manufacturing and Fabrication Shops
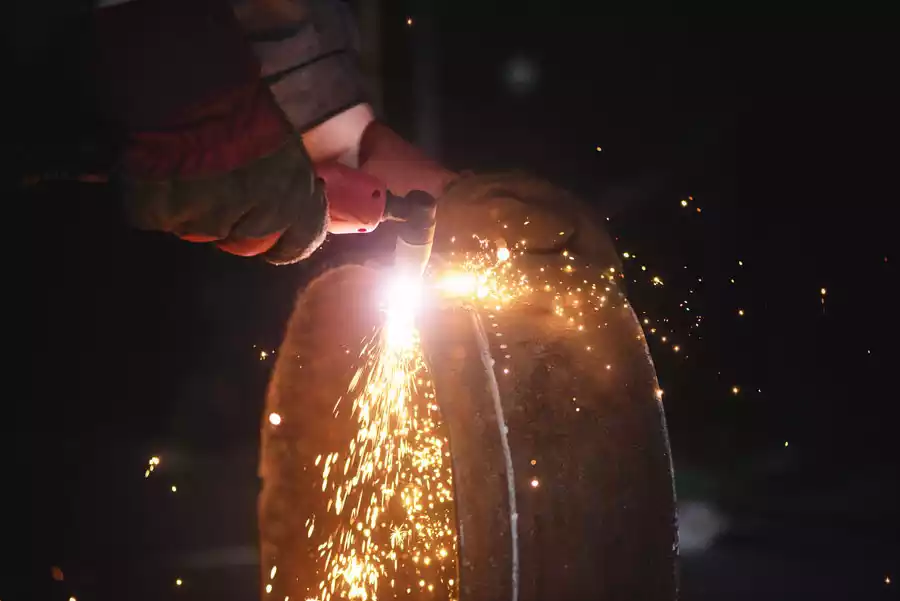
Hand plasma cutting is a powerful and versatile method, but it produces hazardous dust and fumes that require robust air quality controls.
Hand plasma cutting is a widely used thermal metal cutting process in fabrication, manufacturing, maintenance and repair applications. It uses an electrical arc and compressed gas to generate plasma hot enough to melt metal and blow it away. The process is fast, versatile and highly effective for cutting through conductive metals. Hand plasma cutting is commonly used in heavy equipment manufacturing, construction equipment fabrication, railcar production and other transportation equipment manufacturing sectors for tasks such as cutting steel plate, modifying components or disassembling welded assemblies.
While plasma cutting is more controlled than thermal lancing, it still produces high levels of fine metal particulate, toxic fumes, and intense light and noise, especially in manual, mobile workstations. Plasma cutters are frequently used in open, flexible workspaces where source capture may be challenging. As demand for reshored production grows, managing the air quality risks of plasma cutting is essential to protecting workers and maintaining compliance.
Ready to design a cleaner, safer dust collection solution for your hand plasma cutting operation? Talk to a RoboVent solution specialist today to get started.
Solutions for Hand Plasma Cutting Dust and Fume Control
If your facility performs plasma cutting—whether for heavy equipment, infrastructure components, or transportation systems—you need an air quality strategy that matches the intensity and flexibility of your operation. RoboVent designs systems that protect workers, meet regulatory standards and adapt to the realities of modern manufacturing.
Our engineers bring deep experience in dust and fume control for high-temperature metal-cutting processes like hand plasma cutting. Whether you’re working in a small fabrication shop or a large production hall with overhead cranes and mobile workstations, we can deliver a system tailored to your layout and production needs. Our Senturion® dust collector is built to handle heavy metal particulate and noxious fumes generated by heavy industrial processes such as hand plasma cutting. From source capture solutions to ambient air filtration and fume control, our team can design a system for maximum safety, compliance and efficiency.
Air Quality Challenges in Hand Plasma Cutting
While cleaner and more precise than thermal lancing, plasma cutting still introduces significant air quality risks. Manual cutting, especially in open workspaces, can make fume control difficult.
- Fume and Particulate Generation: Plasma cutting vaporizes metal at high temperatures, producing a fine mist of metal oxide particles. Materials such as carbon steel, aluminum, and stainless steel generate different fumes—including hexavalent chromium, manganese, and nickel—depending on the metal and coatings used. These ultrafine particulates are easily inhaled and can penetrate deep into the lungs.
- Coated and Painted Materials: Cutting coated, galvanized, or painted metals produces volatile organic compounds (VOCs), toxic gases, and even cyanide-based byproducts in some cases. These emissions may exceed safe exposure limits in poorly ventilated or high-volume environments.
- Combustible Dust and Sparks: Plasma cutting can generate dry, powdery metal dust and produce sparks that ignite accumulated dust or flammable residues. This introduces fire and explosion hazards, especially when cutting aluminum or magnesium alloys. Sparks and heat generated by hand plasma cutting also pose an ignition risk for metal dust created by other nearby fabrication processes.
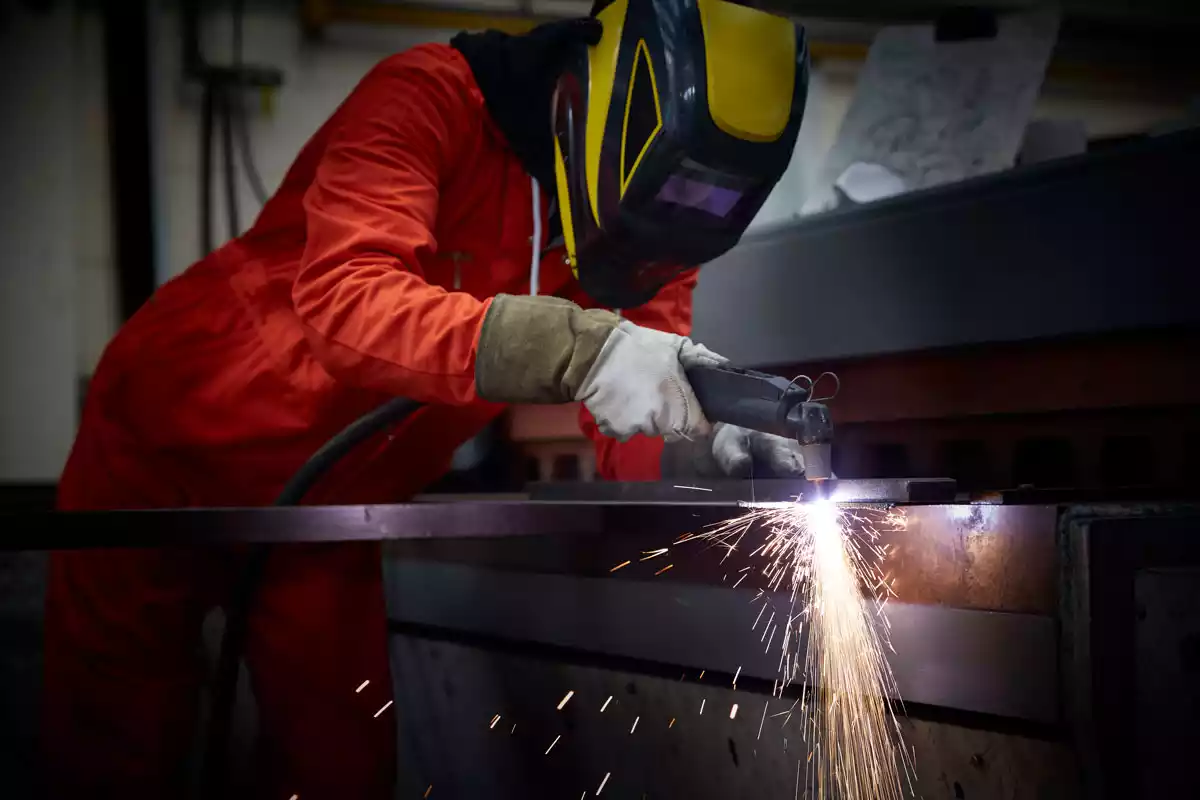
High heat from hand plasma cutting produces fumes containing dangerous metals and metal oxides.
High heat from hand plasma cutting produces fumes containing dangerous metals and metal oxides.
Health and Safety Considerations for Plasma Cutting
Handheld plasma cutters are often used in flexible, open industrial environments where traditional fume extraction is hard to apply. Operators are exposed to a mix of physical, respiratory, and sensory hazards, especially when working on large components in shared spaces.
- Metal fume exposure: Plasma cutting produces fumes that can cause metal fume fever, chronic bronchitis, and an increased risk of lung cancer, especially when cutting stainless steel or galvanized materials.
- Noise, UV radiation, and heat: Plasma arcs generate high-intensity light, extreme localized heat, and loud noise. Prolonged exposure can lead to hearing loss, eye damage and burns without proper protection.
- Toxic gases: Manual plasma cutters can expose workers to ozone, carbon monoxide, and nitrogen oxides, particularly in enclosed spaces or areas with poor ventilation.
Key hand plasma cutting exposure risks include:
- Metal fume fever
- Respiratory illness and lung damage
- Cancer from hexavalent chromium and nickel
- Manganism and other neurological effects from manganese exposure
- Skin, eye and respiratory irritation
- Elevated risk of asthma and sensitization
Regulatory Compliance for Plasma Cutting
Modern hand plasma cutting operations must comply with multiple safety and environmental standards, especially as new facilities are developed under reshoring initiatives.
- Worker Health and Safety: Employers must control worker exposure to metal fumes and gases, including Occupational Safety and Health Administration (OSHA) permissible exposure limits (PELs) for iron oxide, chromium, manganese, nickel and other toxic substances in hand plasma cutting fumes. NIOSH and ACGIH recommend even stricter limits for some substances for long-term health protection.
- Combustible Dust: Plasma cutting of fine metals like aluminum or magnesium may create combustible dust or create ignition hazards for other combustible dust sources. Dust collectors and filtration systems must comply with National Fire Protection Association standards such as NFPA 660, which outlines requirements for dust hazard analysis (DHA), spark control, and explosion prevention. Additional standards such as NFPA 68 (Explosion Protection by Deflagration Venting) and NFPA 69 (Explosion Prevention Systems) may also apply to the dust collection system.
- Environmental: When cutting coated or painted materials, operations may release hazardous air pollutants (HAPs) or VOCs. Proper fume capture and filtration are needed to limit emissions and comply with federal and state air quality regulations, including U.S. Environmental Protection Agency (EPA) Clean Air Act requirements for emission control.
Considerations in Dust and Emission Control for Plasma Cutting
Because plasma cutting is often performed manually on medium to large workpieces in shared or mobile spaces, source capture is not always feasible—especially in high-traffic or multi-use areas. Ambient air filtration is often the most practical and scalable solution, particularly for open-bay facilities using overhead cranes. RoboVent’s Vortex® ductless ambient systems offer flexibility while maintaining OSHA compliance.
In more contained areas—such as prep bays, welding booths or workstations with limited cutting scope—fume arms can be deployed to capture fumes near the arc. These must be positioned carefully to avoid interfering with tools and workflow.
Other important considerations include:
- Spark arrestance: Use a spark arrestance system such as the Delta3 Inline Spark Arrestor to prevent ignition of collected dust from hand plasma cutting and other fabrication processes. Sparks are frequent and hot in plasma cutting environments.
- Fire and explosion protection: Cutting aluminum, magnesium, or coated parts increases combustible dust risk. Equip dust collection systems with explosion protection and active dust collector fire suppression systems and make sure the system complies with NFPA 660 and other relevant standards.
- Filter selection: Choose high-efficiency, flame-retardant dust collector cartridge filters rated for metal particulates. In stainless steel cutting, consider HEPA after-filters. When cutting painted or coated metals, activated carbon after-filters may be recommended for VOC and HAP control.
- Airflow engineering: Maintain consistent airflow across open work zones without obstructing operator movement or overhead equipment. Push-pull ambient systems or distributed ductless units help create clean zones and improve overall safety.
Retractable enclosures: In fixed work areas, retractable enclosures like the DuroRoom™ can help contain fumes and sparks during hand plasma cutting, improving the efficiency of dust and fume control systems while allowing access for tools and equipment.
Contact Us With Your Questions!
SUBSCRIBE TO
BLOG UPDATES