Built to Last, Engineered for Safety: Air Quality Solutions for Heavy Equipment Manufacturing
From bulldozer booms to crane chassis, the machines that shape our world are built through hard, hot, gritty processes: welding, cutting, grinding and machining thick steel into precision parts. In heavy equipment manufacturing, every process has a purpose, and every process has a pollution problem. And right now, the heavy equipment market is booming.
These operations generate metal fumes, toxic gases, oil mists and combustible dust, often in open production spaces where containment is difficult and mobility is essential. Tackling these air quality challenges isn’t just a matter of compliance—it’s about protecting your workforce and keeping operations running smoothly. Let’s take a closer look at the core applications in heavy equipment manufacturing and the clean air solutions that help keep them safe.
RoboVent specializes in engineered air quality solutions built for the real-world demands of heavy industry. Our Senturion® dust collector is purpose-built for high-volume, high-particulate applications like welding, plasma cutting, grinding and abrasive blasting in heavy equipment manufacturing. And with our VentMapping™ Engineering process, we leverage advanced computational and modeling tools to design ambient air filtration solutions tailored to managing weld fume and other contaminants generated while working on large, irregular pieces.
Learn more about Senturion
Learn more about VentMapping
Welding
Manual and robotic MIG, TIG, and flux-core welding are everywhere in heavy equipment production. From robotic welding lines to custom fabrication bays, welding joins together structural frames, arms and attachments made from heavy-gauge carbon or alloyed steel. The right weld fume extraction solution depends on whether you’re using manual welding, robotic welding or a combination of both.
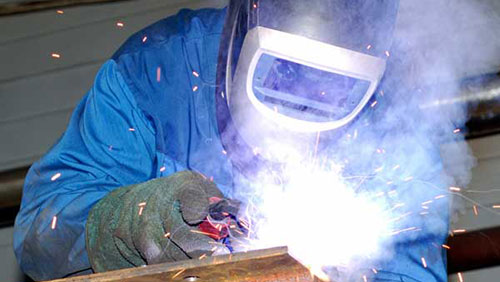
Manual welding of stainless steel produces hazardous fumes containing toxic metals, metal oxides and gases.
Welding on stainless steel and other alloyed materials produces hazardous metal fumes, including hexavalent chromium, manganese and nickel —all of which are associated with serious health risks such as cancer, neurological damage and respiratory illness. These fumes are generated when intense heat vaporizes the base metal or filler material, forming toxic submicron particles. When welding on painted, primed, or coated components, volatile organic compounds (VOCs) and other toxic gases may also be released.
Manual Welding Solutions
In heavy equipment manufacturing, manual welding is often performed on large parts that can’t be enclosed or positioned at fixed stations. Welders may need to move around, under or even inside massive structures, making traditional source capture challenging. But that doesn’t mean fume control has to be compromised. Depending on the process and environment, potential solutions include:
- Fume guns with high-vacuum systems: Hi-vac portable weld fume extractors like the RoboVent ProCube® II pair with fume guns to capture welding fumes directly at the arc. These systems are ideal for mobile welders working on large or irregular components, where conventional arms can’t follow the seam.
- Portable weld fume extractors with articulated extraction arms or backdraft hoods: Where feasible, source capture systems can be used in semi-contained weld cells or at fixed workstations. These allow flexible positioning of the capture point close to the source while keeping obstructions to a minimum. The VentBoss® line has many powerful portable weld fume control options.
- Ambient air filtration systems: In open work bays or large-scale welding environments—especially those with overhead cranes or mobile workstations—ambient filtration systems like RoboVent Vortex® provide background protection, continuously pulling airborne contaminants away from the breathing zone and circulating clean air back into the space. Ambient systems may also be used for secondary air quality control when source capture alone is not adequate to meet permissible exposure limits.
Robotic Welding Solutions
Robotic welding cells are a productivity powerhouse in heavy equipment manufacturing—delivering consistency, speed and quality on heavy-gauge structural components. These systems often run high-amperage welds for long durations, producing significant volumes of ultrafine particulate that can easily spread if not properly contained. Robotic systems need robust, high-performance dust collection solutions that can keep up with the fume load and prevent contaminants from escaping into surrounding work zones.
- Source capture: Where possible, heavy robotic welding applications should be enclosed to keep weld fumes out from propagating through the environment and putting human workers at risk. Smaller components can be enclosed under a traditional hood, such as RoboVent’s Streamline™ Hood. This modular hood system pairs well with RoboVent Spire, a compact and powerful dust collector built specifically for robotic weld fume collection. Larger workpieces can be enclosed under large retractable enclosures, such as those from Duroair. These enclosures keep fumes from large structural components contained and can be retracted for access by overhead cranes or to reconfigure the workspace.
- Ambient filtration: Where pieces cannot easily be contained for robotic welding work, ambient fume extraction is an option. In larger bays or semi-open robotic areas, ducted push-pull systems help maintain directional airflow and prevent cross-contamination between cells. Where overhead space or layout makes ducting impractical, Vortex® ductless units provide flexible placement with powerful airflow control to capture and filter lingering fumes. To ensure proper airflow zoning and maximize effectiveness, RoboVent’s VentMapping® engineering process models your facility’s environment in 3D, identifying optimal system placement, duct paths, and flow rates for total air quality control.
- On-torch extraction: For some robotic applications, on-torch extraction paired with a high-vacuum fume extraction system like RoboVent FlexPro™ is an alternative. A close-capture system for robotic welding, such as RoboVent FlexTrac™, captures weld fumes as they are created, reducing the need for large ambient systems.
Plasma and Oxy-Fuel Cutting
Hand-held plasma and torch cutting are used to shape, modify, or trim parts during fabrication, rework, or disassembly. Plasma and oxy-fuel cutting are essential operations in heavy equipment manufacturing, used to shape, trim, and dismantle large steel components during fabrication or rework. These cutting methods generate intense heat and dense metal fumes, along with ultrafine particulates and toxic gases—especially when working on painted, galvanized or coated materials. Because cutting is often performed manually on oversized parts in open areas, it presents significant challenges for containment and source capture.
Source capture is ideal when the cutting process can be performed at a fixed workstation or in a semi-contained environment. High-vacuum extraction arms with heat-resistant hoods can be positioned near the cut to remove fumes at the source. For high-heat applications such as plasma cutting, take in consideration that source capture also pulls in the heat from the process. Bleed-in air might be needed to keep the temperature at the filter media to the media design criteria.
However, for mobile cutting operations or work on large structural pieces, ambient air filtration is often the more practical solution. RoboVent’s Vortex® ductless floor-mounted ambient filtration units offer flexible deployment around the cutting zone, using a circular airflow pattern to pull contaminated air away from workers and return clean, filtered air to the environment. Facilities with higher volumes of cutting or multiple stations may benefit from a ducted push-pull ambient system designed to create directional airflow throughout the space. RoboVent’s VentMapping® engineering process ensures that airflow patterns and equipment placement are engineered to your facility layout and production flow, maximizing both efficiency and worker safety.
Because hand plasma cutting and oxy-fuel cutting produce sparks, slag and molten debris, all systems must also be designed with fire and explosion protection in mind. Spark arrestors like the Delta3® Inline Spark Arrestor, flame-retardant filters, and explosion protection features should be included as needed to ensure compliance with NFPA 660 and OSHA regulations.
Thermal Lancing
Thermal lancing is one of the most extreme thermal processes used in heavy equipment manufacturing, often employed to cut through thick, hardened or irregular steel components during repair, disassembly or rework. The process generates temperatures exceeding 7,000°F, producing high volumes of smoke and toxic fume, molten slag, sparks and intense heat. Because thermal lancing is typically performed manually on large components in open areas, conventional source capture systems are rarely practical.
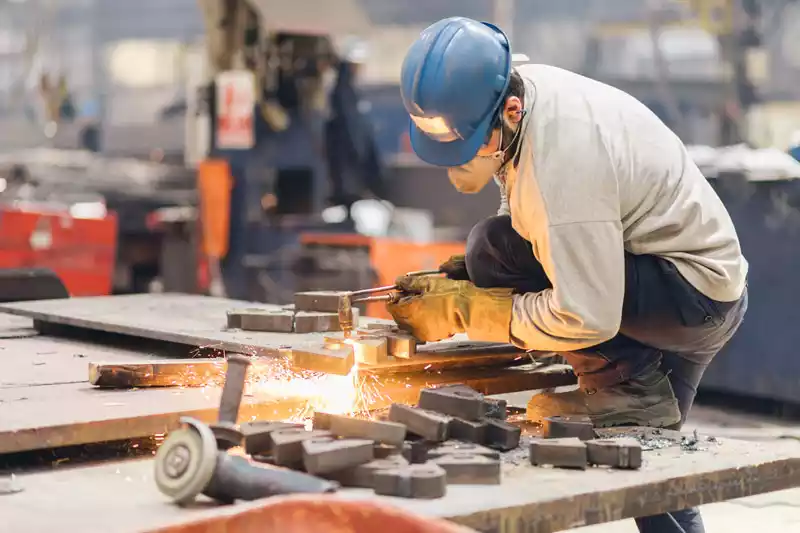
Oxy-fuel and plasma cutting are used to shape, trim and dismantle parts during fabrication, rework or assembly.
Thermal lancing is most often performed in open environments (usually outdoors). In enclosed or semi-enclosed areas, ambient air filtration is usually the most effective strategy for controlling contaminants during thermal lancing. Ductless, floor-mounted units like RoboVent’s Vortex® can be positioned around the work zone to continuously capture and filter airborne fume and particulate. These systems are especially useful in facilities that use overhead cranes or have open layouts where mobility is essential. When higher fume volumes or larger work zones are involved, a ducted push-pull system may be used to establish airflow across the bay and draw contaminants away from the operator’s breathing zone.
If thermal lancing is performed in a semi-contained area—such as a designated prep or teardown zone—localized extraction may be possible using large hoods or backdraft plenums. In either case, all systems must be designed with thermal hazards in mind. Spark control, fire suppression and explosion protection are critical.
Grinding and Surface Prep
Grinding, sanding and other surface prep tasks are common throughout heavy equipment manufacturing, from weld cleanup and deburring to prepping parts for painting or assembly. These operations generate large amounts of fine, dry metal dust that can quickly become airborne and spread across the facility, especially when performed on large components or in open areas.
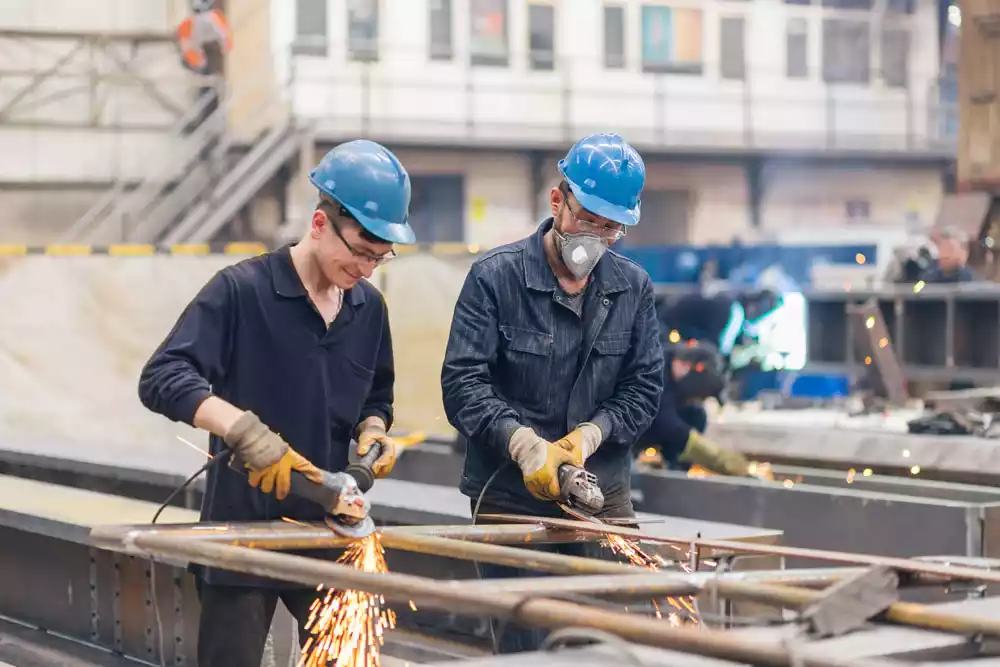
Manual grinding, sanding and deburring generate heavy metal dust along with sparks.
When grinding is performed at fixed stations or on smaller parts, source capture is typically the best approach. Downdraft tables, backdraft benches or fume arms can help pull dust away from the operator’s breathing zone and minimize dispersion. RoboVent offers a range of configurable source capture systems designed specifically for these high-dust prep tasks. Because grinding dust is heavier than weld fume, it tends to fall downward toward the floor instead of rising into the air. This makes downdraft an effective choice for most grinding applications.
In more open environments, such as when workers are grinding large structural components or using portable tools, shrouds can be placed around the grinding wheels, connected to a hi-vac dust collector. Ambient air filtration systems may be used as a secondary system to help maintain safe background air quality throughout the facility.
Because many of the dusts produced during grinding—such as steel, aluminum or coated material particulate—can be combustible, all grinding dust collection systems should be designed with appropriate fire and explosion safety features. Filter media must also be selected based on the dust load and particle characteristics to ensure effective, long-lasting performance.
Machining and Drilling
Machining operations such as drilling, milling and boring are frequently used in heavy equipment manufacturing to finish components with tight tolerances, often after welding or forming processes. These operations may generate fine metal dust, composite particulate or oil mist, depending on the materials being worked and whether coolants or lubricants are used.
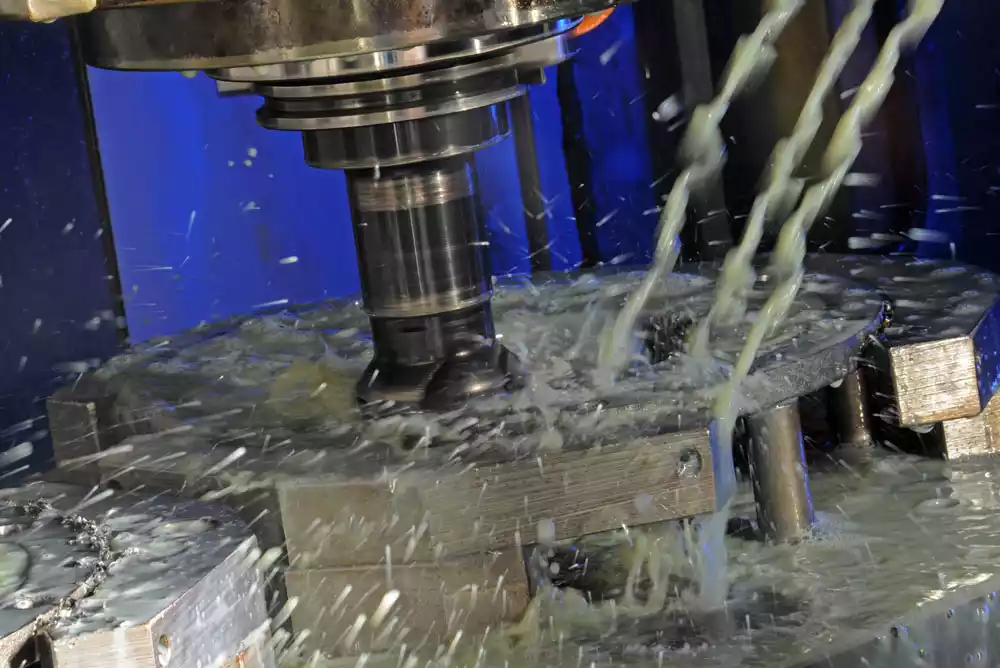
Lubricants, coolants and metalworking fluids (MFWs) used in machining, milling and drilling generate oil mists and oily particulate, requiring specialized
Dry machining and metal-on-metal operations can create dry airborne dust that presents both respiratory hazards and combustible dust risks. Where dry particulate is the primary concern, source capture systems such as backdraft hoods or downdraft tables can help contain contaminants at the point of generation. Enclosed CNC cells or dedicated robotic machining bays can be ducted directly to the dust collector for efficient source capture. A cartridge dust collector works well for dry machining dust collection.
When machining processes use water- or oil-based coolants, the resulting aerosolized oil mist can present a different set of challenges. Oil mists may carry hazardous additives, create slip-and-fall hazards or cause skin and eye irritation. Traditional dust collector cartridge filters are designed for collection of dry (or mostly dry) particulate; even oleophobic filter media is only meant to handle slightly oily dust, not aerosolized mists. For wet machining applications, high-efficiency oil mist collectors like RoboVent Clarion® are recommended. These systems use packed-bed filter media that allows oil mists to coalesce on the surface and drain off, carrying fine particulates with them.
Abrasive Blasting
In heavy equipment manufacturing (including construction equipment, railway components and tractor-trailer manufacturing), abrasive blasting plays a key role in surface preparation. Large steel components—such as booms, buckets, frames and chassis assemblies—are typically blasted to remove mill scale, rust or fabrication residues after welding and before coating and painting. This ensures stronger paint adhesion and longer-lasting corrosion resistance in the finished product.
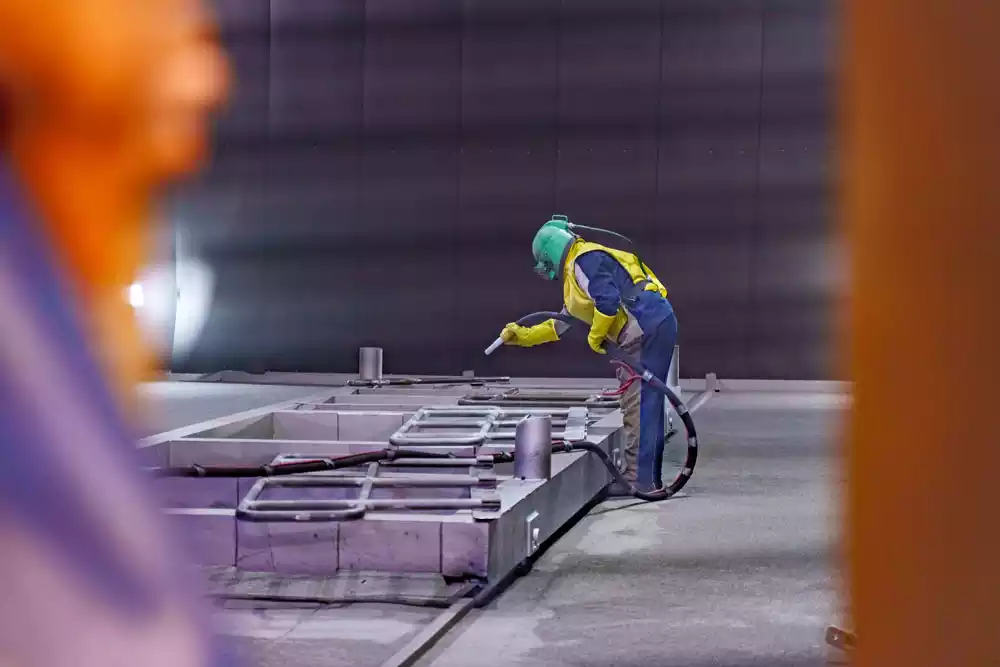
Abrasive blasting and surface finishing produce large volumes of airborne dust.
But blasting these large, often irregular parts generates massive volumes of airborne dust. The abrasive media itself, combined with loosened rust, scale and coatings, creates a highly mobile cloud of fine particulate that can quickly spread throughout the facility. When blasting is performed on coated or primed parts, additional hazards may be introduced, including toxic metal dust (like lead or chromium) and VOC-laden coating residues.
In production environments for heavy equipment, abrasive blasting is typically done in semi-enclosed bays or large blast rooms; full containment may not be feasible due to the size of the components. In these settings, high-volume source capture systems are essential to control airborne dust at the point of generation. Ductwork, filtration media and collection systems must be designed to withstand abrasive, high-dust environments with large particulate loads.
Ambient air filtration may also be used to supplement source capture—especially in open production areas or when blasting operations are adjacent to other fabrication processes. Effective dust control not only protects workers’ health and safety, but also helps maintain a cleaner environment for downstream operations like painting and final assembly, where residual dust can compromise quality.
Dust Collection for Heavy Equipment Manufacturing
While these processes are common across the heavy equipment industry, every facility is different. Some manufacturers run high-throughput robotic welding lines to maximize efficiency and consistency. Others specialize in custom fabrication or low-volume, high-mix production where mobility and flexibility are key. Some plants operate in legacy buildings with aging infrastructure and limited ventilation options, while others are designing new facilities with advanced automation and sustainability goals.
That’s why RoboVent never takes a one-size-fits-all approach. We start every project by taking the time to understand your specific operation—your layout, process flow, materials, workforce needs, and regulatory obligations. For ambient solutions, we apply our state-of-the-art VentMapping™ engineering process to model airflow and contaminant propagation and determine the most effective placement for dust collectors–with or without ductwork. From there, we design smart, scalable air quality solutions that support your goals for safety, compliance, and productivity.
Need help designing a clean air solution for your heavy equipment manufacturing operation?
Contact a RoboVent solution specialist today. We’re ready.
Contact Us With Your Questions!
SUBSCRIBE TO
BLOG UPDATES