THE COMPLETE GUIDE TO WELDING
FUME EXTRACTION SYSTEMS:
HOW (AND WHY) TO KEEP YOUR FACILITY AIR CLEAN AND SAFE
CHAPTER SIX: FILTER SELECTION FOR WELD FUMES
Filter selection is an important component of both source capture and ambient air filtration system design. Filters for weld fumes must be capable of capturing the very small, sub-micron particulate created by thermal processes such as welding. In this section, we will focus on filter selection for cartridge dust collectors used for weld fume control.
What kind of filters are used for weld fume capture?
The filtration system must be equipped with filters capable of removing the very small particulate created by thermal processes such as welding. For most applications, it is recommended that the filtration system be capable of removing 85% or more of the smallest particulate; when working with highly toxic materials such as hexavalent chromium (produced when welding stainless steel), a capture rate of 95% or greater may be advisable. Generally, that will require a filter with a rating of at least MERV 15 for general weld fume and a rating of MERV 16 or higher when welding stainless steel.
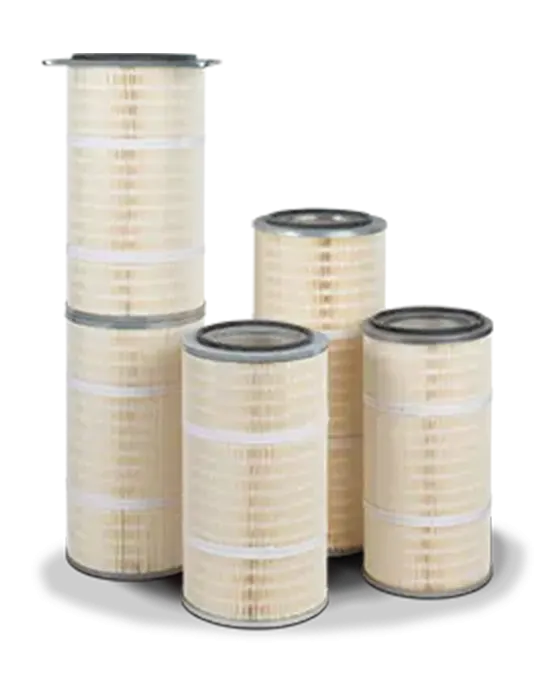
Particle size distribution for weld fumes depends on the welding process, but particles are largely in the 60-200 nm (0.06 – 0.2 micron) range, though they can cluster together into complex chains or structures in the 5-10 micron range. Weld fume particulate may also be mixed with larger particles from co-existing processes such as cutting or grinding and environmental contaminants such as dust, pollen and mold spores.. Always check with your local regulations to ensure that the filtration system reduces contaminant levels below the required PEL; air quality testing may be advised after the system is in place to ensure that the filtration system is adequate for the level and type of fume produced.
What are MERV ratings for filters?
A majority of dry particulate filters are rated using the MERV (Minimum Efficiency Reporting Value) rating system, which assigns values of 1 - 16. The filter’s MERV rating tells you how efficiently it captures particulate within different size bands (3 – 10 microns, 1 – 3 microns and 0.3 – 1.0 microns). The higher the MERV rating, the more efficiently the filter captures smaller particulate.
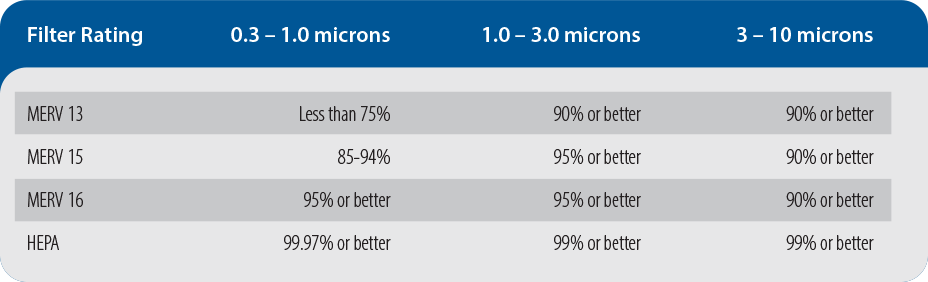
What are HEPA filters?
Above MERV 16, filters are classified as High-Efficiency Particulate Air (HEPA) filters. HEPA filters must be able to capture 99.97% or more of particulate in the 0.3 - 1.0 micron range. HEPA filtration may be advised when welding stainless steel or materials with coatings that produce highly dangerous contaminants.
How is the MERV or HEPA rating determined for air filters?
ANSI/ASHRAE Standard 52.2 provides testing requirements for air filters, which are used to determine the MERV rating. Results of independent testing should always be obtained to ensure that filters meet system requirements.
What are mechanical filters, and when are they used?
Both MERV and HEPA filters remove dry particulate using mechanical filtration. Particles are captured by the fine fibers of the filter media through a combination of direct impact/interception, electrostatic attraction/sieving and diffusion. Both cartridge dust collectors and baghouse dust collectors utilize mechanical filtration. Filters for cartridge-style dust collection systems come in a variety of ratings, typically starting at MERV 11 all the way up to MERV 16. For welding, it is recommended to choose filters with a higher MERV rating (MERV 15 or above). For a progressive filtration solution, the dust collector may be fitted with a pre-filter at the intake and HEPA or activated carbon after-filters.
Most HVAC filters also rely on mechanical filtration (though some may be impregnated with activated carbon or use electrostatic filtration). In general, it is not recommended that companies rely on the HVAC system for weld fume removal. If the primary dust collection system is able to reduce weld fume contamination below acceptable levels, no special consideration may be needed for HVAC filter selection. If the HVAC system is required to collect fugitive fume left by the primary dust collection system, HVAC filters should also be MERV 15 or higher.
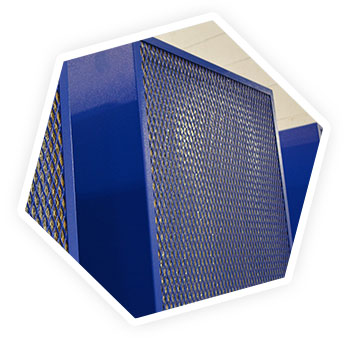
Can an electrostatic precipitator be used for weld fume?
Electrostatic precipitators are not typically used for weld fume collection due to the large volume of fume created during welding. They are more commonly used for collection of cigarette smoke or diesel exhaust. These devices use ionization to create charged air within the collector, which imparts a charge to incoming particles. As particles move between plates with opposite charges, they are attracted to the plates and pulled out of the airstream. Filtration efficiency depends on several factors, including air velocity, collector plate spacing, the cleanliness of the plates, and the magnitude of ionization. They require a high level of maintenance to keep collector plates clean, which makes them less than ideal for weld fume collection. A double-pass system with two sections of collector plates may be needed for complete particle capture.
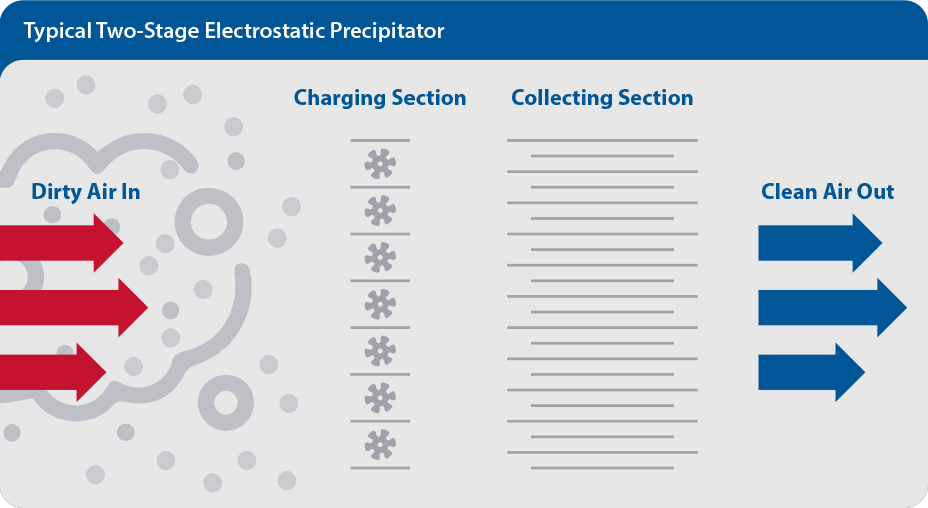
What is molecular filtration?
Molecular filtration is used to capture gas-phase and vaporous contaminants that may be present in weld fumes, such as VOCs or shielding gases. Molecular filtration may or may not be required as part of the weld fume collection strategy; typically, this will only be used if high levels of noxious gases or vapors are present along with the dry particulate in the weld fume. The most common type of molecular filtration used for welding and metalworking is activated carbon. Activated carbon works by adsorption, in which molecules are attracted to the surface of the material and held by chemical or physical bonding. Activated carbon and other adsorptive materials have thousands of “micropores” to maximize the available surface area for adsorption. Specialized materials may be used to remove specific molecular contaminants.
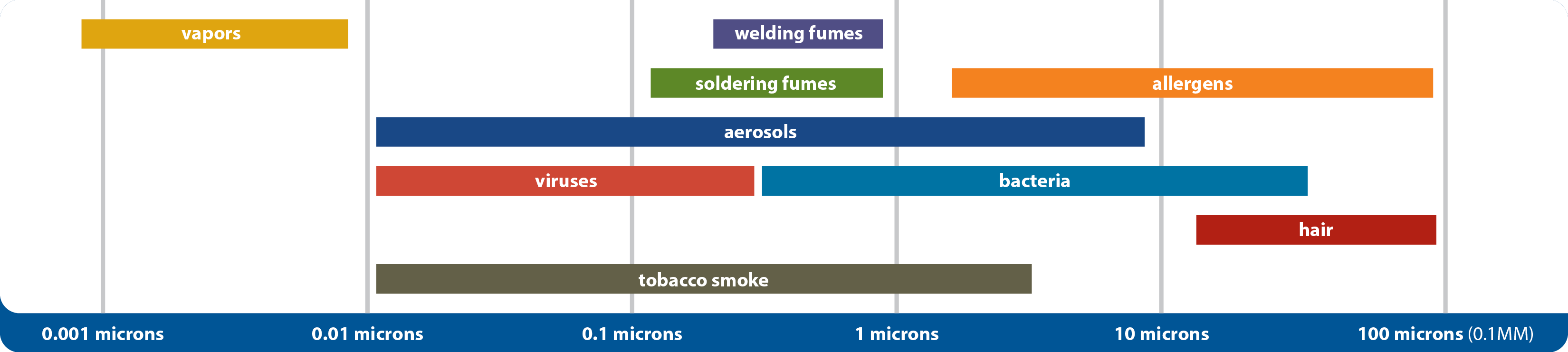
What is progressive filtration?
In a progressive filtration system, multiple filters are used, each having a higher efficiency rating than the previous. This allows larger particles to be removed by lower-priced filters, extending filter life for filters with higher efficiencies. Progressive filtration may be desirable when weld fume is mixed with coarser dust from other processes, such as metal grinding. For example, a MERV 6 filter may be used as a first-stage disposable filter to remove the larger particles, followed by a MERV 15 filter to remove fine contaminants. When welding materials containing chromium, nickel, or other highly toxic and regulated substances, a HEPA filter may be recommended for final filtration. If gas-phase or vaporous contaminants are present, a molecular filter such as activated carbon may also be used. Progressive filtration may also be achieved by using a cyclone dust collector for first-stage filtration before passing air into a cartridge dust collector.
A typical filter stack for progressive filtration may be:
- Washable metal mesh spark arrestor and/or centrifugal spark arrestor
- Cartridge, pocket or cell-style dry filters
- Molecular filter (e.g., activated carbon)
- HEPA after filter
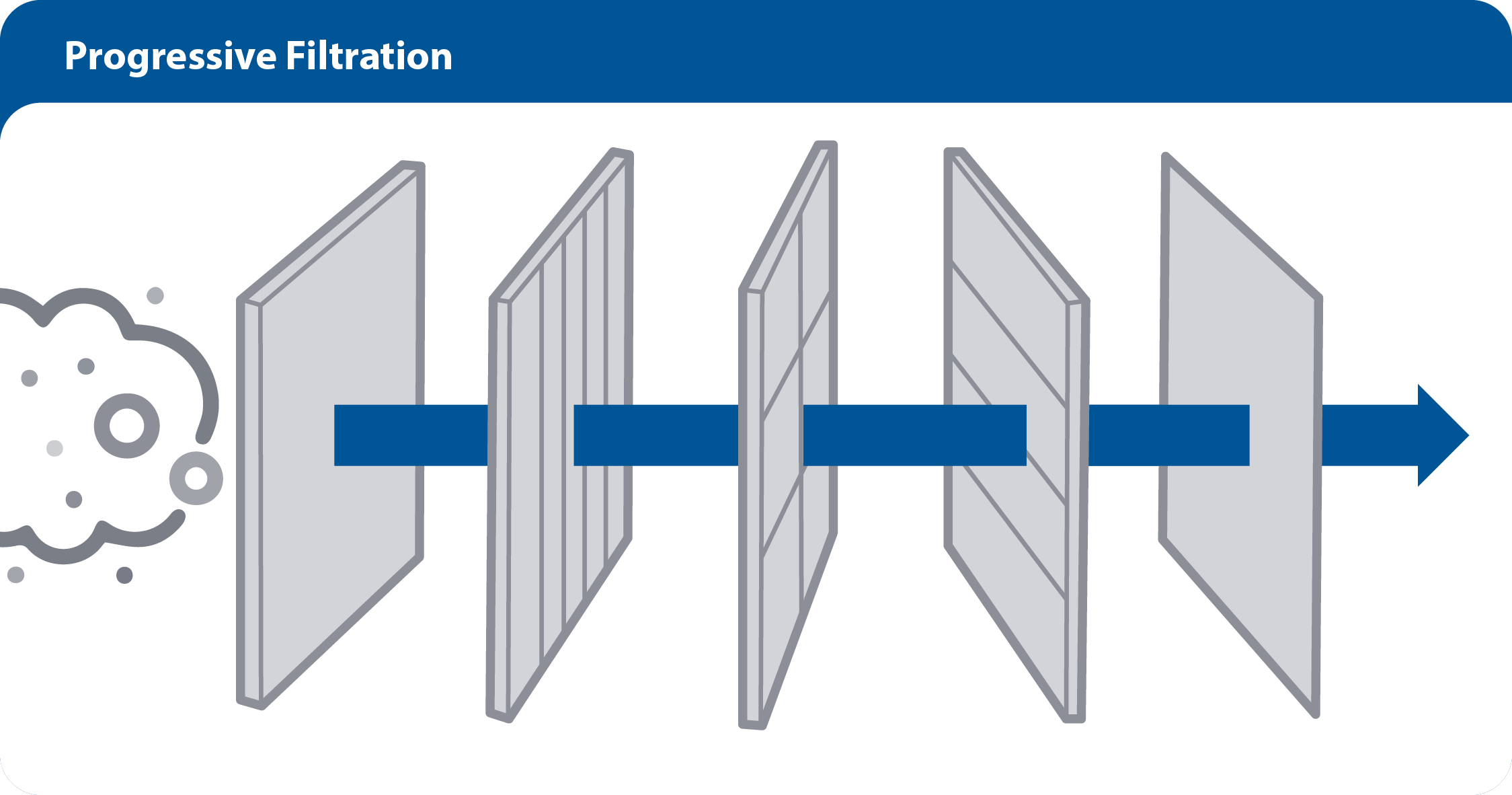
TALK TO AN EXPERT
Want to learn more? Talk to a dust, mist and fume expert today by filling out the fields below.